Our X-ray inspection allows a large number of applications for the highest of demands. Concealed particles, defects on or in the glass or under package components, for example the crimp, are reliably detected. We offer X-ray inspection solutions for the laboratory as well as for high-speed inline inspection for up to 600 products/minute. X-ray inspection can also be combined with our other inspection technologies.
Why X-ray inspection is important
The two most important Critical Process Quality Attributes in the glass container handling process are the maintaining of sterility and the indemnification of foreign particle absence within a closed container. We have developed a foreign particle detection system based on X-ray. A low energy X-ray source, together with a highly sophisticated image recognition and processing technology, allows the detecting of non-visible particles in lyo cakes, powders, emulsions and in suspensions. It is usable for vials, ampoules and syringes of different sizes. The X-ray based system also detects glass defects under a vial crimp cap and functional defects such as poor needle alignment of syringes.
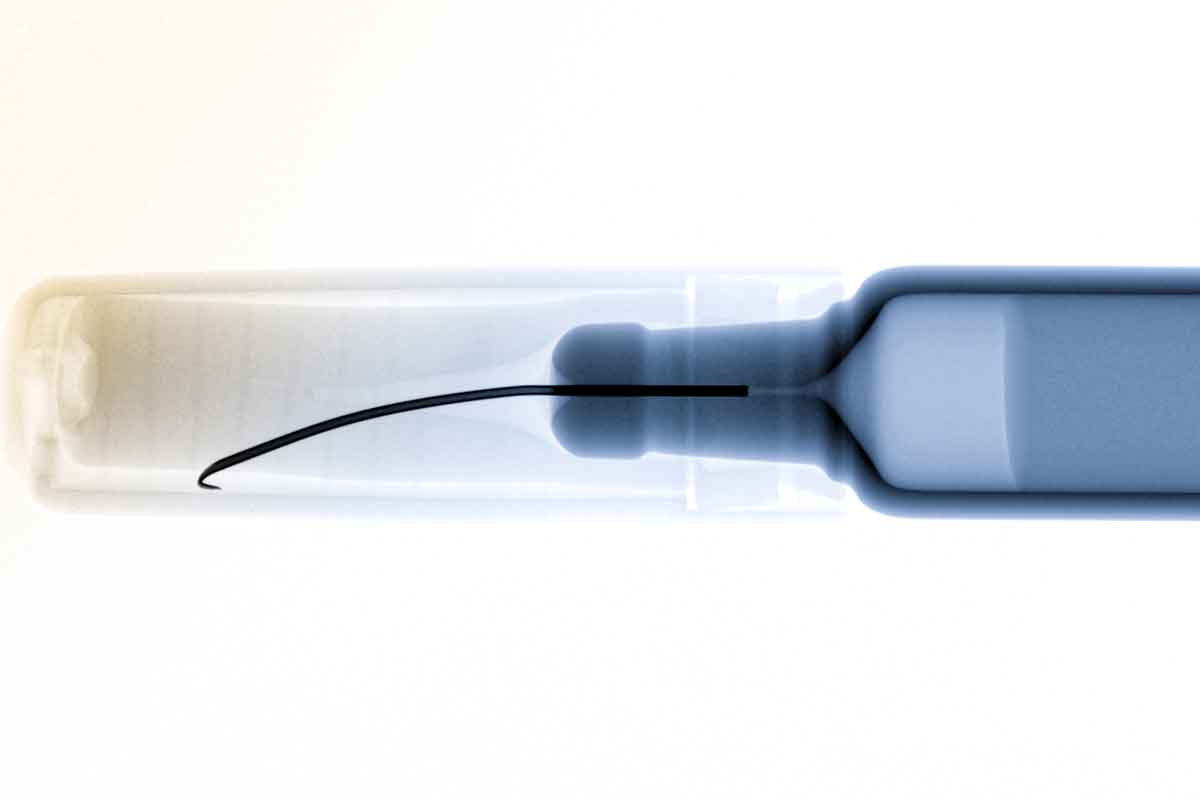
Working principle of X-ray inspection
While passing through the low-energy X-ray field, any samples and their potential defects, are magnified onto a fast CMOS detector array. The resulting size of the sample or defect image can be calculated due to the distance relations between X-ray source / sample and sample / detector.
The detector converts the incoming X-rays into light and transfers the picture onto the CMOS diode array. The results are immediately available and are evaluated instantaneously, allowing the processing of high production speeds.
X-ray is an imaging technology which creates 2D images that can then be inspected for defects. In X-ray imaging, not only the detector needs to fulfill certain requirements but also the X-ray source itself is required to obtain some crucial properties. These properties are defined by the field of application. In short the technology defines two types of X-ray tubes. The first one is the closed tube design producing radiation with a focus between 800µm and 1500µm and the second is the micro-focus tube design with a focus between 1µm to 5 µm. In general it is the focus diameter that defines the spatial resolution of such an imaging system or the smallest object which can be made visible in such a picture.
X-ray inspection possibilities
A wide variety of X-ray inspection tasks is possible with regards to pharmaceutical products. Applications are:
- Crack detection
- Foreign particle inspection
- Functional defects
Area imaging
The second technique is the area X-ray camera which works similar to a simple photo camera. Here the object will be penetrated by the radiation, attenuated by the object and the result is captured as a grey scale image on a large X-ray sensitive diode array. This scanning process produces 2D as well as 3D pictures, but 3D is widely used in material research and in medical examinations.
The area imaging technique today is fast and reliable because pictures are taken during the complete standstill of a sample and beam. With this technology a picture can be produced and evaluated within 100 ms or even faster compared to several seconds using scanning technology.

Advantages of our X-ray inspection solution
- Foreign particle detection in lyo cakes, powders, suspensions and emulsions
- Inspection of glass defects e.g. rim defects under the vial crimp cap
- Inspection of functional defects e.g. needle alignment inspection on prefilled syringes
- High flexibility with regard to object sizes and container dimensions
- Detection of a wide variety of foreign particles including glass, metal, plastics and many other materials
- High resolution X-ray detector to identify smallest particles (metal ≥ 70 µm)
- Low energy X-ray source to ensure product integrity (experience due to stability tests)
- Absolute safety conditions for users according to the low energy of the X-ray source (µW emission power range)