Our differential pressure test methods allow a wide range of applications with the highest requirements in terms of container closure integrity testing. The non-destructive leak testing is ideal for a wide range of packaging types for life science, food & beverage and cans & aerosols.
Why Differential Pressure Methods
Almost all combinations of products and packaging materials are suitable for leak testing with differential pressure methods. The leak test can be carried out for liquid, lyophilized or powdered products. Packaging materials such as vials, syringes, ampoules, LVPs or devices can be inspected. In addition to testing the primary packaging itself, vacuum decay can also be applied to auto-injectors and other devices containing sterile packaging or a sterile reservoir. This requires a thorough analysis of the components and close collaboration during the packaging development process. We provide support throughout these phases and help you to select the right leak testing method.
General working principle
The differential pressure methods are based on a gas exchange between the test chamber and the test sample. The sample is placed into the test chamber which is hermetically sealed prior to testing. After the chamber is sealed, either pressure or vacuum is applied inside the test chamber. After a time period of pressure stabilization, the differential pressure is measured. In the case of a leakage, the sample allows a gas exchange between the test sample and the test chamber which leads to a specific pressure change identifying a leak. Depending on the packaging and product type, the relevant test method is selected and adjusted.
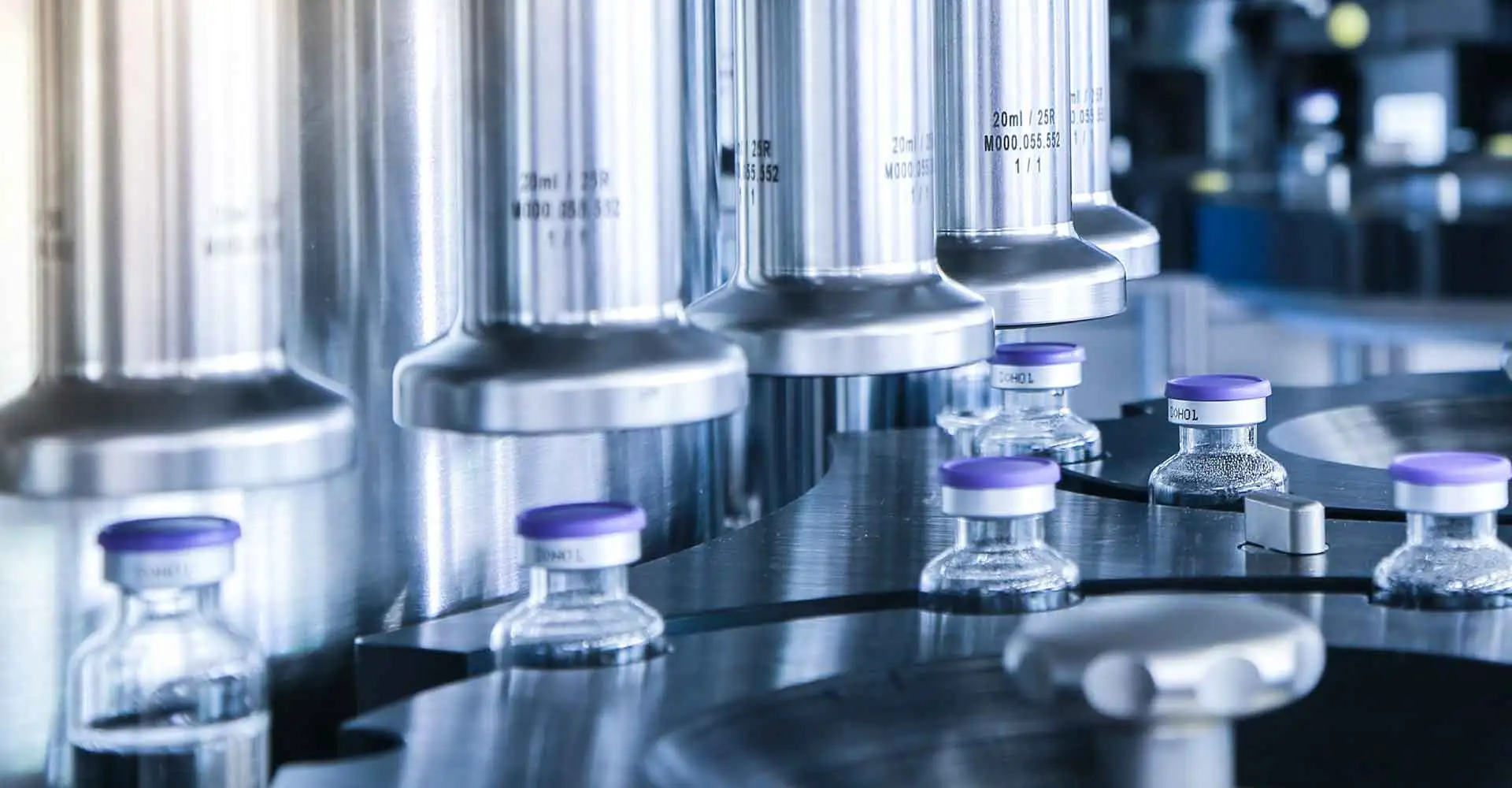
LFC method®
WILCO Liquid Filled Container LFC method® – the advanced vacuum decay method.

As with other differential pressure methods, the LFC method® is based on a gas exchange between the container and the test chamber. In order to test liquid filled containers, the LFC method® operates at a deep vacuum level. This vacuum level allows liquids to vaporize and requires the use of custom, proprietary sensors developed by WILCO AG to make the precise differential pressure measurements. The LFC method® is optimized to check for leaks in both the headspace as well as the liquid phase of a container.
The vaporization of the liquid has an extreme impact on the differential pressure inside the chamber. Therefore, even smallest leak covered with liquid can be detected.
NB: Not all liquids provide the same vaporization effect. Consequently, we offer tests in our laboratories in order to determine the probability of detection.
Advantages
- Non-destructive test method for 100% inspection
- Versatile use in terms of packaging and product types and sizes
- Deterministic test methods acc. USP<1207>
- Quantitative determination of leakage
- No modified headspace required
- No conductivity of liquid required
- High sensitivity
- Entire product is tested
- Applicable for liquid and lyo products
- Applicable for alcohols
Vacuum decay method
The vacuum decay leak test is suitable for a large number of applications.
By using the vacuum decay method, the air around the container is evacuated at certain pre-defined vacuum levels, after hermetically sealing the test chamber. In the presence of a leak, air/gas from inside the container will flow into the test chamber reducing the vacuum level. The standard vacuum decay technology is suitable for leak detection on lyophilized or powdered products filled in rigid containers and for testing the closure integrity of vials (cap/crimping system).
Advantages
- Non-destructive test method for 100% inspection
- Versatile use in terms of packaging and product types and sizes
- Deterministic test methods acc. USP<1207>
- Quantitative determination of leakage
- No modified headspace required
- Entire product is tested
Pressure decay method
The pressure decay leak test is suitable for a wide variety of containers.
The pressure decay method is based on a gas exchange between the test chamber and the container. The volume around the container will be filled with sterile air at a certain pre-defined pressure level. A reduction of the pressure level will indicate the presence of a leak due to the corresponding gas transfer.
Advantages
- Non-destructive test method for 100% inspection
- Versatile use in terms of packaging and product types and sizes
- Deterministic test methods acc. USP<1207>
- Quantitative determination of leakage
- No modified headspace required
- Entire product is tested
Looking for more information about our CCIT capabilities?
We are happy to advise you personally.