Regulatory requirements and Best Practice for leak testing in BFS production: A practical guide
Blow-Fill-Seal (BFS) technology, widely used in the pharmaceutical industry, allows for the efficient, aseptic manufacturing of liquid medications. Renowned for its robust sterility assurance, BFS minimizes contamination risks and supports product integrity. However, ensuring the integrity of BFS containers through precise leak testing is crucial for maintaining sterility, efficacy, and regulatory compliance.
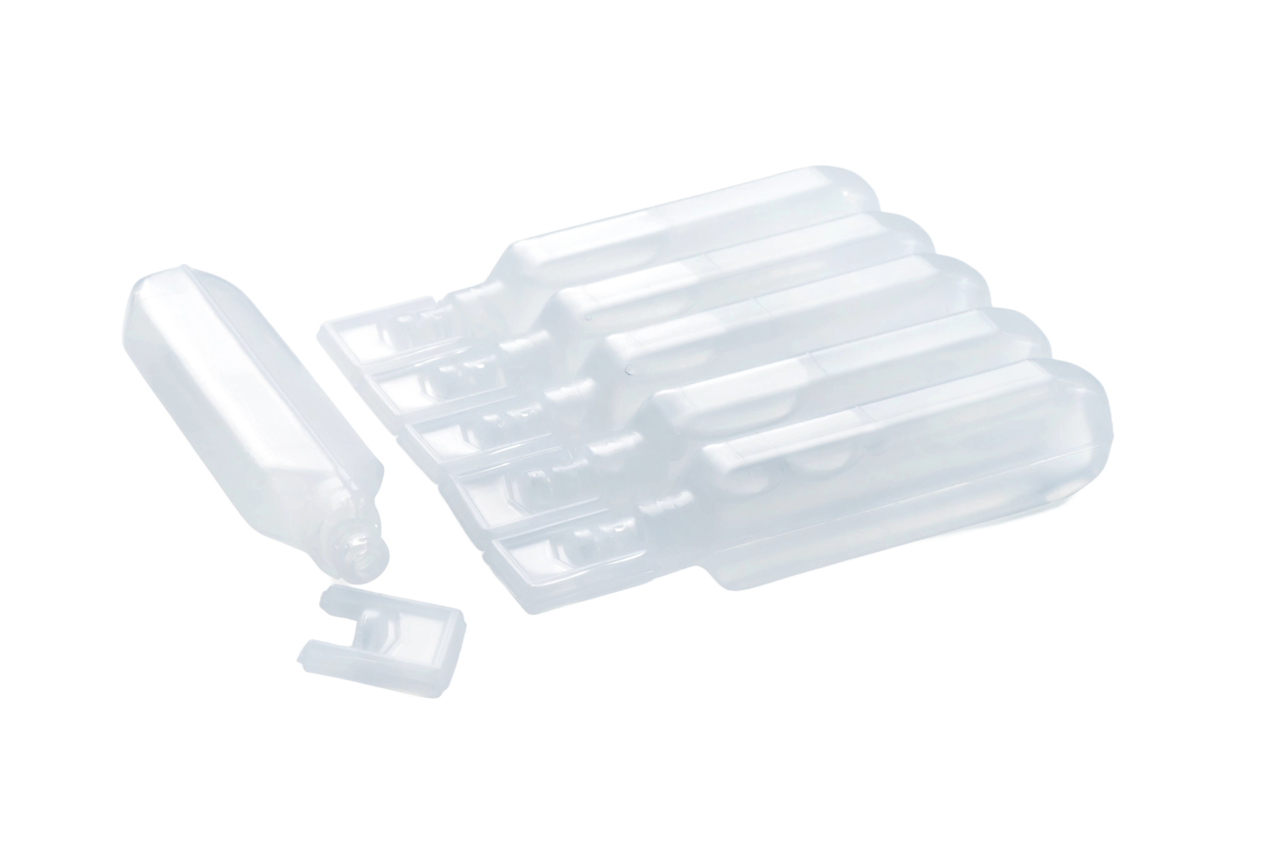
Container Closure Integrity Testing (CCIT) is fundamental to BFS production, as leaks in BFS containers can result in microbial contamination, product spoilage, and loss of drug value. The primary goal of leak testing is to confirm the integrity of the container throughout the product’s lifecycle.
Leak testing methods for BFS products must be sensitive enough to detect leaks that could compromise sterility, and consistent with regulatory guidelines. Typical leak testing techniques are vacuum decay and high-voltage leak detection (HVLD) methods. Each method has specific advantages and limitations that make them suitable for certain BFS applications and product types.
Regulatory Landscape for BFS Leak Testing
The global regulatory framework for CCIT in BFS production is governed by agencies such as the United States Food and Drug Administration (FDA) and the European Medicines Agency (EMA). While specific requirements can vary by region, common themes and standards exist for ensuring that BFS containers remain secure and maintain sterility.
FDA Regulations
The FDA requires CCIT as part of aseptic processing regulations under 21 CFR Part 211, which mandates that BFS systems meet stringent sterility and packaging integrity standards. Key points include:
- Sterility Assurance: All drug packaging must protect contents from contamination. All containers must demonstrate sterility via CCIT.
- CCIT in Stability Testing: FDA guidance suggests that CCIT should be performed during stability studies to confirm container integrity over time.
- Method Validation: The FDA also stresses the need for validated CCIT methods to ensure reliable and reproducible results, emphasizing the selection of appropriate leak detection techniques.
EMA Regulations
The EMA’s standards align closely with those of the FDA but place additional emphasis on the environmental impact of BFS processes. The EMA requires:
- Integrity Validation: Per EU GMP Annex 1, BFS containers must undergo rigorous CCIT as part of production process validation.
- Routine Monitoring: Regular leak testing is expected, particularly for critical BFS products, as part of ongoing quality assurance.
- Risk-Based Approaches: EU GMP Annex 1 contains a stronger focus on Risk Management and the implementation of a Contamination Control Strategy.
- Contamination Control Strategy (CCS): A formal testing protocol that outlines the site-wide approach to prevent finished product contamination is necessary.
In-depth guidance is now available for the risk-based development and performance of aseptic processing simulation (APS) or media fill inspection, crucial in verifying aseptic system sterility. Striving for zero growth, any contamination leads to APS failure and triggers a series of at least three consecutive repeat tests following investigation and corrective measures to ensure process control restoration.
Regulatory impact on inspection tasks: Best Practices
Container Closure Integrity Testing (CCIT) and Process Analytical Technologies (PAT) are pivotal for verifying the efficacy of contamination prevention measures and form critical components of contamination control systems. Annex 1 emphasizes the importance of evaluating and controlling critical parameters and variables that impact seal integrity, particularly for final containers closed by fusion, such as Blow-Fill-Seal (BFS), Form-Fill-Seal (FFS), Small and Large Volume Parenteral (SVP & LVP) bags, and glass or plastic ampoules.
For containers like glass ampoules, BFS units, and small-volume containers (≤100 mL), 100% integrity testing using validated methods is required to ensure sterility. In contrast, for large-volume containers (>100 mL) closed by fusion, reduced sampling may be acceptable if justified scientifically and supported by data that demonstrate process consistency and robust process control. It is also explicitly noted that visual inspection is not an acceptable method for integrity testing.
Selection of the Appropriate Testing Method
Choosing the most appropriate testing method depends on the BFS container type, fill material, and product sensitivity. Some methods include:
Advanced Vacuum Decay: The WILCO LFC method ®
A robust, non-destructive method suitable for BFS containers. Based on a gas exchange mechanism between the container and the test chamber, this method operates at a deep vacuum level, enabling the vaporization of liquids and facilitating precise measurement of differential pressure. The highly optimized LFC method® is designed to detect leaks in both the headspace and the liquid area of the container, providing an efficient and comprehensive inspection solution. Clogging effects of protein or high sucrose solutions have to be taken into consideration.
+ Non-destructive testing of BFS and FFS packaging
+ Applicable for various shapes and sizes of BFS containers
+ Suitable for oily and non-conductive liquids
+ Ideal for any filling level
+ Deterministic test method preferred according to USP 1207
+ Data handling in compliance with 21 CFR part 11
High Voltage Leak Detection (HVLD)
Effective for liquid-filled BFS products, HVLD detects leaks based on dielectric changes in the solution.
HVLD requires a conductive liquid inside the container behind the leak to function effectively. Containers made of electrically insulating materials, such as the HDPE or LDPE commonly used in BFS, are compatible. However, low-conductivity liquids or air behind the leak—common in small-volume BFS ampoules (< 1-2 mL)—can significantly reduce accuracy or render measurement impossible. Environmental factors like humidity and temperature can also impact the precision of HVLD results. Differential pressure testing, by contrast, can be applied to a broader range of materials and container types.
Process Analytical Technologies (PAT)
While manual visual inspection remains common for media fill inspections today, upcoming Process Analytical Technologies (PAT) present promising alternatives, offering efficiencies in time, resources, and data-driven decisions that align well with Annex 1's scientific standards.
Each method must be validated to ensure it meets sensitivity requirements and is compatible with the BFS container's physical properties.
Implementing Risk-Based Testing Strategies
A risk-based approach aligns with regulatory guidance, focusing on BFS products most susceptible to leak issues due to design, fill volume, or product sensitivity. By categorizing products based on their risk profiles, manufacturers can allocate testing resources efficiently, balancing regulatory compliance with operational practicality.
Validation and Routine Testing
Validation ensures that CCIT methods consistently detect leaks within a specified range. Validation processes for example can include the following
- Method Sensitivity Testing: Defining the smallest detectable leak size. 10 μm has established itself in the industry.
- Reproducibility: Confirming that leak detection results are consistent across multiple test runs and batches.
- Routine Testing: Incorporating validated CCIT methods into the BFS production line to ensure continuous container integrity monitoring.
Meeting Data Integrity and Documentation Standards
According to 21 CFR part 11, regulatory authorities stipulate data integrity in leak testing documentation. The data generated during CCIT must be accurate, secure, and traceable, covering all aspects of the testing process, from setup to results. Considerations include:
- Documentation of Test Parameters: Recording all test parameters, such as environmental conditions, container size, and fill type.
- Audit Trail: Maintaining an audit trail for all data entries to ensure traceability and compliance.
- Change Control and Quality Management: Any changes in testing methodology or equipment should follow change control procedures to ensure they don’t impact BFS product integrity.
Ensuring container closure integrity in BFS production is essential for regulatory compliance and patient safety. If you’re looking to strengthen your BFS production’s leak testing protocols or need guidance on regulatory requirements, our team of experts is here to help. With deep industry knowledge having supplied over 100 BFS inline inspection machines and state-of-the-art testing solutions, we can support your facility in designing, implementing, and validating the most effective leak testing methods.
Get more information
Contact us today for a consultation and discover how we can optimize your leak testing processes, ensuring regulatory compliance and product integrity from the start. Whether you’re building a new testing program or enhancing an existing one, our solutions are tailored to meet your specific BFS production needs.
Do you need support with your BSF inspection?
We are happy to advise you personally.